
Background: WoodCraft Furnishings (not the real name *), a reputable furniture manufacturer, noticed a significant decrease in production efficiency in one of their key departments. The assembly line responsible for crafting intricate wooden designs experienced delays and bottlenecks, affecting the overall production timeline. Concerned about meeting customer demands, the management decided to apply the 5 Whys method to identify and resolve the root cause of the issue.
The 5 Whys In Action
1st Why: Issue: Production delays in the wooden design assembly line. Question: Why are there delays in the assembly line?
Answer: The assembly line workers are frequently waiting for specific tools and materials.
2nd Why: Issue: Workers are waiting for specific tools and materials. Question: Why are the tools and materials not readily available?
Answer: The inventory of specialized tools and materials is disorganized, making it difficult for workers to locate them quickly.
3rd Why: Issue: Inventory of tools and materials is disorganized. Question: Why is the inventory disorganized?
Answer: There is no standardized system for organizing and restocking tools and materials after use.
4th Why: Issue: No standardized system for organizing and restocking tools and materials. Question: Why hasn’t a standardized system been implemented?
Answer: There was no awareness of the issue, and the workers did not report it because they assumed it was the responsibility of another department.
5th Why: Issue: Lack of awareness and communication regarding tool and material organization. Question: Why is there a lack of awareness and communication?
Answer: There are no regular communication channels between the assembly line workers and the inventory management team, leading to a lack of information flow.
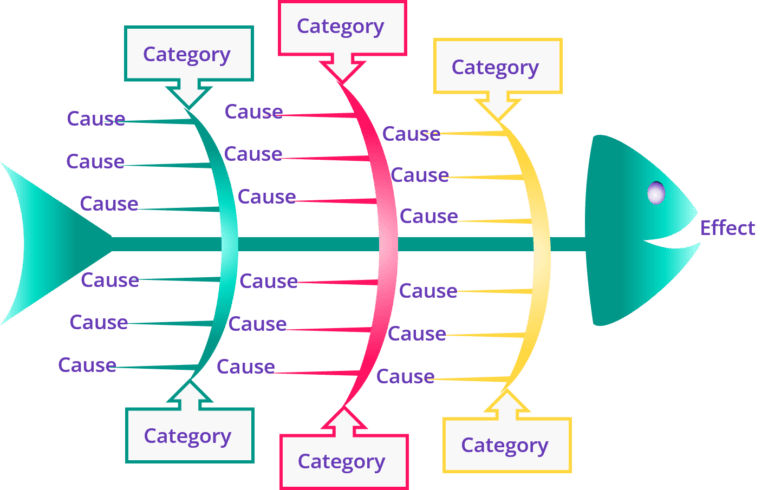
Now What?
The solution or Action: WoodCraft Furnishings implemented a daily team meeting between the assembly line workers and the inventory management team. During these meetings, workers discuss any issues related to tools and materials, ensuring that the inventory management team is promptly informed of restocking needs. Additionally, a visual management system was introduced, clearly indicating where each tool and material should be placed after use.
* Names, characters, places, and/or incidents with any resemblance to actual persons, living or dead, businesses, companies, events, and/or locales is/are entirely coincidental.