In a well-known city, amidst the constant hustle and bustle, stood Mercy Health (not the real name *), struggling with dangerous disorganization. Determined to provide better patient care, and to achieve greater worker satisfaction, they embarked on a transformative journey – implementing the Lean 6S methodology. This methodology promised streamlined operations, making work safer and easier for the staff, and enhanced patient experiences. Through the principles of Sort, Set in Order, Shine, Standardize, Sustain, and Safety the hospital was seeking a change for the better. But, the path to efficiency was riddled with obstacles.
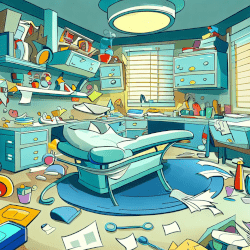
Sorting the Storm
Here at Mercy Health, chaos reigned supreme. Medical supplies were scattered, patient records were misplaced, and communication between departments was muddled. Sorting through this mess was the first challenge. The hospital formed a dedicated team, conducting thorough assessments to identify essential items. Obsolete equipment was discarded, and organization began to take root.
Setting New Foundations
Setting in Order proved to be a daunting task. Hospital staff struggled to find necessary equipment promptly, affecting response times. The solution was ingenious: color-coded storage systems and digital inventory management. Each department had its designated color, making it easier for staff to locate supplies swiftly. Additionally, digital tracking systems were implemented to monitor inventory levels in real time.
Shining Amidst Crisis
Shine, the cleanliness aspect posed significant hurdles. Hospital hygiene was paramount, yet cleaning schedules were inconsistent. The hospital administration invested in staff training, emphasizing the importance of cleanliness and implementing daily cleaning routines. Regular audits were conducted, ensuring adherence to cleanliness protocols. The hospital now gleamed with a sense of order and hygiene.
Standardizing Excellence
Standardizing procedures across departments was a colossal challenge. Each department had its own unique workflow, leading to confusion and inefficiency. A hospital-wide initiative was launched to create unified protocols. Task forces were formed, composed of experienced staff members who collaborated to establish standardized procedures. Clear, concise guidelines were developed, ensuring consistency in patient care and administrative tasks.
Sustaining the Momentum
Maintaining the newfound efficiency was an ongoing struggle. Staff turnover, complacency, and resistance to change threatened the progress made. Mercy Health introduced a comprehensive training program for new hires, ensuring they were well-versed in Lean 6S principles. Regular workshops and refresher courses were conducted for existing staff, reinforcing the importance of the methodology. Employee recognition programs were established, acknowledging and rewarding sustained adherence to Lean 6S standards.
Ensuring Safety
The final piece of the puzzle was Safety. Patient safety was paramount, and ensuring a safe environment was non-negotiable. The hospital invested in ergonomic equipment, reducing the risk of staff injuries. Safety drills and training sessions were conducted regularly, preparing staff for emergencies. Transparent communication channels were established, enabling employees to report safety concerns promptly.
A Hospital Transformed
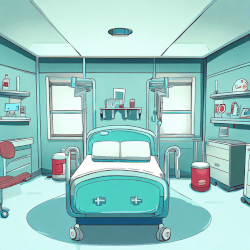
Through dedication, perseverance, and strategic problem-solving, Mercy Health overcame the obstacles and transformed into a beacon of efficiency and patient care. Lean 6S became more than a methodology; it became the hospital’s way of life.
* Names, characters, places, and/or incidents with any resemblance to actual persons, living or dead, businesses, companies, events, and/or locales is/are entirely coincidental.